WHY FORTIPHY™ XVD?
FortiPhy™ XVD (Xcelerated Vapor Deposition) Technology delivers smaller, more consistent nanoparticles while eliminating 90% of the macroparticle defects, cracks and pinholes common to conventional wear and corrosion coatings. The nearly defect-free coating barrier produced by FortiPhy™ XVD Technology is far superior.
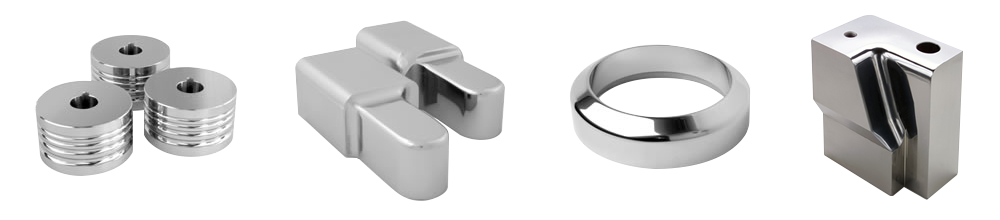
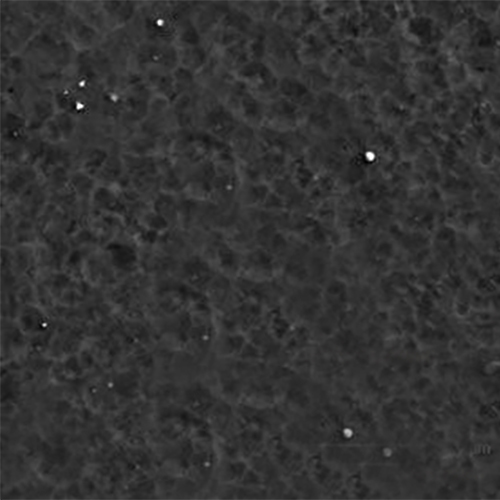
FORTIPHY™ XVD
Nearly defect-free
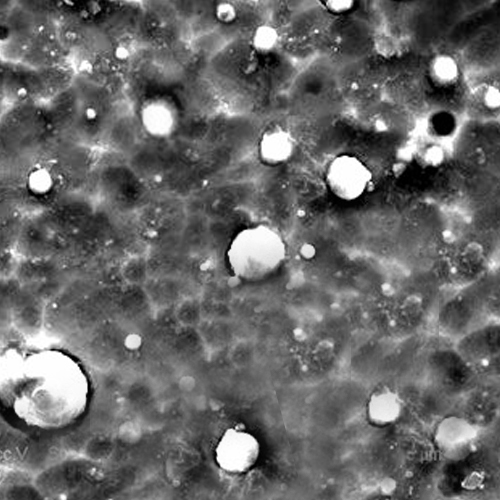
Conventional PVD
Many macroparticle defects and pinholes
ultra-hard
The FortiPhy™ XVD process delivers near-diamond hardness, shielding even the hardest substrate materials. XVD’s more dense and tighter molecular structure delivers the lower surface energy required for higher lubricity, smoother sliding and faster release.
super bond strength
Proven in the lab and in real use application, FortiPhy™ XVD’s adhesion level is 2-3 times stronger than conventional coatings, significantly reducing the peeling, cracking and scratching responsible for most coating failures.
ultra-thin
FortiPhy™ XVD coating thicknesses are precise and controlled, providing exact conformance to fine surface details so tighter tolerances can be met and intended dimensions of components can be preserved.
corrosion protection
FortiPhy™ XVD Technology eliminates 90% of the macroparticle defects, cracks and pinholes common to conventional wear and corrosion coatings.
The U.S. Army chose 12 competing technologies for testing and evaluation. Of the 12 systems examined, Phygen FortiPhy XVD provided the best corrosion and wear protection.
non-toxic, earth-friendly
green is good
FortiPhy™ XVD coatings are deposited in a chemical-free process inside an enclosed vacuum chamber and are completely inert. Environmental exposure to the toxic chemicals found in plating and bath processes is completely eliminated.
Did you know?
Hard chrome plating is now banned by EU/REACH regulations, impacting businesses around the world. FortiPhy™ XVD is an ideal alternative and fully compliant. We have also achieved FDA and USDA certifications.
fortiphy™ xvd
surface enhancement options
FORTIPHY™ XVD
Chromium Nitride
FORTIPHY™ XVD
Aluminum Chromium Nitride
FORTIPHY™ XVD
SILICON Carbide
FORTIPHY™ XVD
CrN + PLASMA ION NITRIDE
FORTIPHY™ XVD
AlCrN + PLASMA ION NITRIDE
FORTIPHY™ XVD
diamond-like carbon