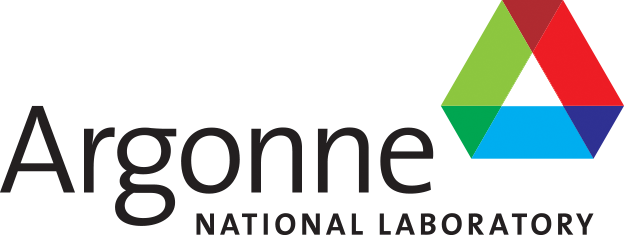
Dr. John B. Woodford, PhD, Tribologist at Argonne National Laboratory, answers questions about tool wear resistance.
First of all, what is Tribology?
Tribology is the study of friction and wear phenomena.
How do you test for wear?
That depends upon the type of wear. In general, a test is chosen that mimics a specific type of motion and environment; e.g., for sliding wear I would use either a pin-on-disc test or a reciprocating sliding test, either run dry or in the presence of lubricants or other fluids. Other tests are used for abrasive wear and rolling contact.
In your experience, what are factors that contribute to wear in metal-on-metal applications?
That depends upon the load and speed regime for the application. In general, surface roughness, chemical properties of the metal(s), and toughness of the material will all contribute. In the absence of lubricant, a common sliding wear mechanism is the growth and removal of surface oxides. That is, suppose the native oxide on the metal is easily worn away. As it is removed, the fresh metal surface oxidizes anew. Although the base metal may be highly wear-resistant, and although the metal oxide may normally prevent further oxidation (as is the case with stainless steel), the combination of oxidation and wear can bring about rapid removal of material. This can be particularly pronounced in cases where the metal oxide is hard enough to act as an abrasive against the base metal.
Under higher loads, failure can occur by so-called scuffing, in which the two surfaces adhere so strongly to each other that they don’t separate before being severely deformed. Unlubricated metal-on-metal contacts can scuff very easily, and because contact severity is higher at the “peaks” of a rough surface, scuffing will take place even more readily there.
What are the best ways to reduce wear?
In general, keep the surfaces from contacting each other. That’s the role of conventional lubricants. Where this isn’t possible, keep the surfaces from having only localized and severe contact; i.e., reduce the surface roughness. Changing the surface chemistry so that, for example, surface oxides are adherent and wear-resistant can help, as will increasing surface toughness.
How do surface finish, hardness, and the composition of the substrate itself contribute to wear resistance?
As alluded to above, surface finish can decrease contact severity, reducing the chance of scuffing. A hard surface is generally less prone to abrasive wear; e.g., from metal oxide wear debris. Substrate composition is important because of oxidation resistance and, by extension, any chemical interaction with the environment.
What are the characteristics of a good coating?
First and foremost, adhesion to the substrate. After that it will depend upon the application. For example, a good coating for cutting tools will not react with the material to be cut at high temperatures, will not break down on heating, and will be hard and tough. A good coating for a mold or a stamping die will not adhere to the workpiece. A good coating for a piston ring in an engine will have inherently low friction and be resistant to sliding wear. For each of these, the critical characteristic is that they stay where they’re put.
Why do coatings fail?
If a contact is particularly severe, even the toughest coating eventually can be worn away. Most frequently, however, coatings fail by delamination — by separating from the substrate. Extremely hard coatings may be more prone to separation if they are at all brittle. If the load is high enough to deform the substrate more than the coating can withstand, the coating will crack. At this point, if coating fragments come off the substrate, they will act as an abrasive in the contact area, thus speeding wear.
How does the use of PVD CrN compare to other coatings?
PVD CrN is not as widely used as TiN or TiAlN, because conventional CrN coatings are generally not as wear-resistant as TiAlN and not as well-understood as TiN.
What has been your experience with Phygen’s patented coatings?
Several years ago, I tested them in reciprocating sliding against hardened steel in Fischer-Tropsch diesel fuel. The coatings themselves did not measurably wear.