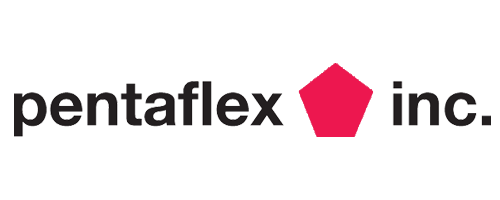
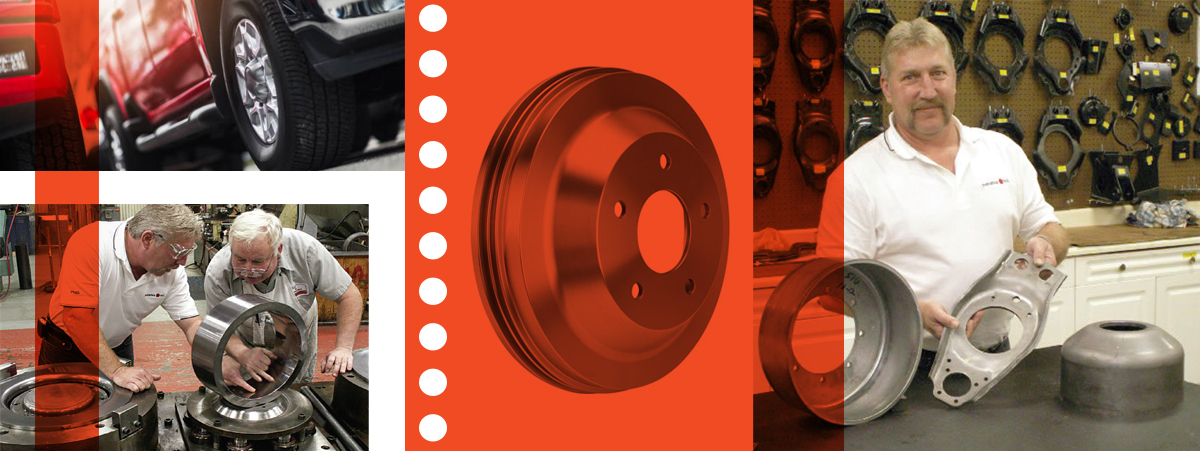
PROBLEM
Pentaflex, a contract metal stamping manufacturer, was experiencing galling and premature buildup that limited its productivity making brake drums. The company tried thermal diffusion, titanium nitride and several other treatments, but some processes would pull carbon from the tool and shorten its life. Re-polishing the tooling each time cost the company at least four hours of downtime.
Solution
Coatings used previously at Pentaflex wore out within 900 hits. By treating the tooling with Phygen FortiPhy XVD, the company achieved continuous runs of more than 37,000 impressions without a polishing downtime incident. Pentaflex is now moving toward adopting FortiPhy XVD for all its stamping operations, and has eliminated problems with galling, chipping and flaking. Increased uptime translates to greater productivity and profitability.
productivity increase
It really is possible
Pentaflex saves between $14,000 and $20,000 per year in reduced downtime and tooling repair expenses. At the time this update was published, the company had produced more than 37,000 parts without a major polishing downtime incident. Also, by eliminating premature buildup, FortiPhy XVD has helped Pentaflex increase production speed of thicker parts made in a hydraulic press.
“At this time, we are heading toward using FortiPhy™ for all our coating needs. Phygen really knows their business. Any time we discuss difficult applications, they always seem to know exactly what part of the tooling to concentrate on.”