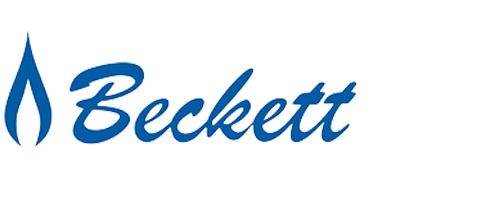
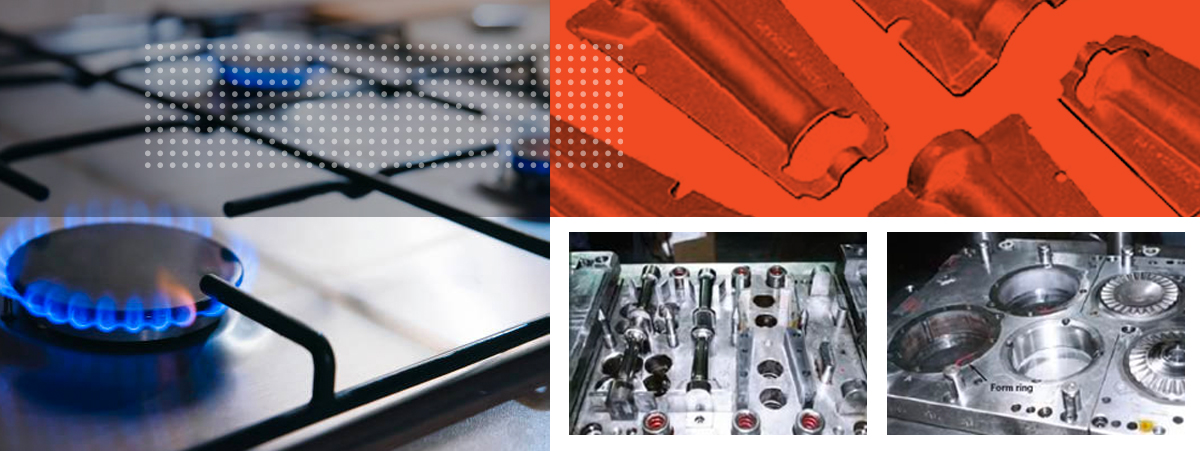

PROBLEM
Beckett Gas makes gas burner products for water heaters and furnaces. Its in-house production line turns out 30 million parts each year. One stamping form had to be sharpened after 60,000 to 80,000 parts. Using powdered metal tool steel and adding a PVD coating increased tool life, but the dies would shrink during the hot coating process.

Solution
Tool and die foreman Rick Roth learned that ForthiPhy™ XVD technology is applied at much lower temperatures, and contacted Phygen to try it for himself. Just as he hoped, the advanced surface treatment did not cause any tool distortion and made the stamping forms even stronger—increasing the number of hits between sharpenings by another 25 percent.

It really is possible
hit increase
After his initial success, Roth had another application in mind: dies used to stamp tough, abrasive, aluminized sheet steel. In that process, tools with a hot-applied thermal-diffusion coating made 400,000 hits before the corners were destroyed. The same forms with FortiPhy XVD made 600,000 hits without the risk of dimensional change and rework hot coatings can cause.
unit increase
“Now that we’ve converted one die, we’ll continue to send tools there, about one tool a month, until we convert nearly every hot-coated tool to FortiPhy XVD.”