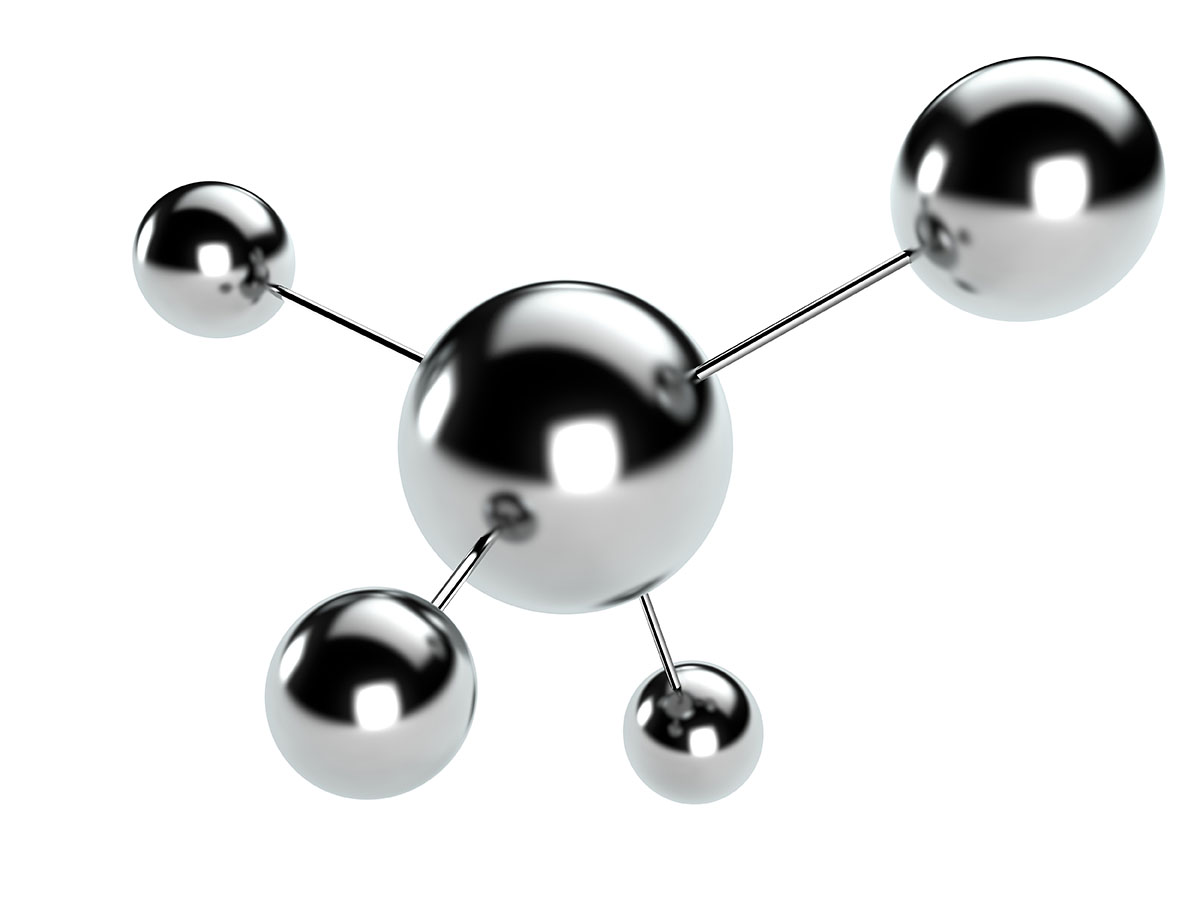
FortiPhy™ XVD: The Complete Story
AUTHORS:
Dave Bell, Eric Bell
It’s time to think beyond even the best, newest conventional PVD coatings, because it’s 50-year old technology. FortiPhy™ XVD is the breakthrough surface armor you need to win the war on wear.
a breakthrough scientific advance
Phygen’s patented FortiPhy™ XVD (Xcelerated Vapor Deposition) technology is based upon a breakthrough innovation in plasma acceleration science. FortiPhy™ XVD incorporates Phygen’s Nanoperfection™ technology which delivers smaller, more consistent nanoparticles while eliminating 90% of the macroparticle flaws and surface defects common to conventional PVD surface coatings. The nearly defect-free nanocrystalline structure produced by FortiPhy™ XVD Technology is far superior to conventional PVD, delivering levels of performance and endurance never before thought possible.
a breakthrough scientific advance
Phygen’s patented FortiPhy™ XVD (Xcelerated Vapor Deposition) technology is based upon a breakthrough innovation in plasma acceleration science. FortiPhy™ XVD incorporates Phygen’s Nanoperfection™ technology which delivers smaller, more consistent nanoparticles while eliminating 90% of the macroparticle flaws and surface defects common to conventional PVD surface coatings. The nearly defect-free nanocrystalline structure produced by FortiPhy™ XVD Technology is far superior to conventional PVD, delivering levels of performance and endurance never before thought possible.
fewer defects means fewer problems
Surface defects, impurities, pits, porosity, edge build-up, and inconsistent coverage from other coatings lead to unreliable quality. They can also lead to reduced throughput, more operator error and adjustment, and increased replacement or repair costs.
When compared to PVD, the XVD (Xcelerated Vapor Deposition) process delivers higher plasma density and an intense, low energy ion bombardment during coating deposition, offering performance improvements that far exceed conventional PVD. Benefits include unprecedented toughness and lubricity, high-strength adhesion, as well as outstanding uniformity.
FortiPhy™ XVD technology allows deposition of a wide variety of coatings (metals, alloys, and compounds) which exhibit extreme hardness and toughness superior to that of the best conventional PVD-based coating. FortiPhy™ XVD surface coating technology provides a combination of superior coating properties by creating a dense, non-columnar coating structure having the highest possible adhesion level.
diamond-like hardness
Coating microstructure is precisely controlled by our patented process parameters. As a result, FortiPhy™ XVD constitutes a single-phase, stoichiometric, nanocrystalline surface having a dense, highly textured structure. The fine-grained structure and high cohesive strength of FortiPhy™ XVD surface enhancement permits deposition of extremely tough and hard coatings with much higher abrasive wear resistance than provided by conventional PVD processes.
Unlike hot-processed CVD (chemical vapor deposition) and TD (thermal diffusion) coatings, which combine with carbon molecules within the substrate to form a hard layer, FortiPhy™ XVD is a chemically complete tool coating, applied to a surface using a special high-adhesion process. Typical CVD and TD coatings are applied at temperatures above 1800°F in order to increase diffusion activity within the substrate. During the hot coating process, carbon atoms move to the surface and combine with the coating material to form a third compound. This can produce a hard coating but there are drawbacks. Only a limited amount carbon in the substrate is available to migrate to the surface, and it can travel only a short distance. This means that as tools and coatings wear, a second application of the coating usually lasts only about 70 percent as long as the first application. A third application generally will have a useful life that is only 30 percent as great as the original tool coating. After that, free carbon is all “used up.” When no additional carbon can be leached to the surface, the re-coating process ceases to provide any benefit. Furthermore, decarburization of the substrate weakens material near the surface, thereby increasing the likelihood of chipping.
No carbon is leached from the substrate
FortiPhy™ XVD does not require diffusion within the substrate to build a hard coating. Instead, our patented process, with its exceptional level of process control, applies a chemically stoichiometric layer of nano-sized particles onto the surface. No carbon or other molecules are leached from the substrate. This means that every re-coat of tools, dies or components treated with FortiPhy™ XVD has the same toughness and lasts as long as the first. More importantly, no decarburization or weakening of the substrate occurs. Tool life is extended, and chemical composition of the substrate remains unchanged, regardless of rework.
FortiPhy™ XVD is an industrial surface armor that far outperforms conventional PVD. It is not a decorative coating. However, its appearance may be enhanced, if necessary, by the addition of a TiN or other color overlay. While FortiPhy™ XVD is primarily intended to reduce wear in severe stress and temperature applications, it also is highly corrosion resistant. In a recent test, a purposely substandard application of very thin and porous FortiPhy™ XVD on mild steel provided significant protection by cutting the corrosion rate and by creating a passivity range with a pitting potential of more than 800mV. In the same test, a uniform coating of FortiPhy™ XVD further decreased the corrosion rate by several orders of value. In real-world applications, FortiPhy provides unprecedented corrosion protection. In an injection mold, for example, a coating of FortiPhy™ XVD provided a 600-percent increase in the life of mold vents that previously had been destroyed by caustic thermoplastic byproducts.