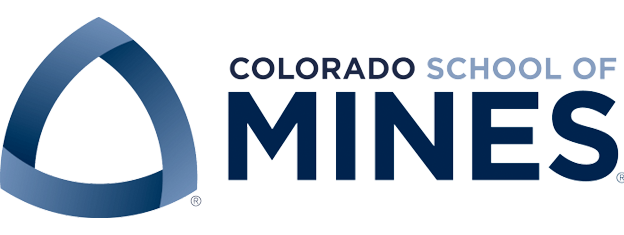
AUTHORS:
John J. Moore, PhD, Colorado School of Mines
Dr. John J. Moore answers a few questions about surface engineering. Dr. Moore is Trustees’ Professor, Head of the department of Metallurgical and Materials Engineering, and Director of the Advanced Coatings and Surface Engineering Laboratory at the Colorado School of Mines, Golden, Colorado.
1. First of all, what is surface engineering?
Surface engineering is any method that modifies the surface of a material or component such that the physical, mechanical and/or chemical properties of that surface are changed to provide a range of properties that meet specified performance criteria. There are many surface modification techniques available. These include: controlled heat treatment (diffusion coatings) such as carburizing and nitro-carburizing; physical vapor deposition (PVD); chemical vapor deposition (CVD coatings); plasma enhanced processes, such as plasma-enhanced CVD (PECVD); ion implantation; surface (shot) peening to provide a compressive stress in the surface and electro-deposition.
2. How do you test for wear?
There are several methods that can be used to test for wear of coatings and films. For thick diffusion coatings (0.1-2 mm) there are standardized tests defined by ASTMS, such as the sand abrasion test that records the wear rate against abrasive sand particles, which are abraded against the coating at a certain load/force. For thin films (05-10 microns) a scratch-adhesion test is very popular. In this test, the film is moved against a sharp indenter at a constant speed with increasing load. The load that indicates film decohesion (failure) is termed the critical load (Lc). The value of Lc also is a measure of the adhesion strength of the coating or film. Reciprocating wear tests are conducted on the same scratch-adhesion tester in which the load on the indenter is usually some small fraction, e.g., 10% of Lc, and the indenter is moved backwards and forwards across the film.
The extent of wear is a measure of the amount of material removed under these reciprocating scratching conditions. One variation of this reciprocating wear test is the “pin-on-disc” test in which a sharp pin or indenter is moved across the surface of the film or coating at constant load in a circular motion. The pin can be a sharp indenter or take the form of a knife blade. There also are several micro-wear testers or microtribometers on the market that are capable of measuring wear in very thin films, say 10-50 nm. In each of these wear tests, the amount of wear usually is measured by determining the volume of material removed as a function of time and loading.
3. In your experience, what are the factors that contribute to wear in metal-on-metal applications?
These are the main factors:
- Difference in hardness of the wear faces
- Roughness
- Coefficient of friction/lubrication of the interface
- Load/pressure
- Atmosphere: conjoint effects of corrosion/humidity, oxidation,
- Poor adhesion
4. What are the best ways to reduce wear?
First you should minimize the factors cited above. Once you have done that, you can still gain significant improvement in reducing wear by:
- Self-lubricating/adaptive coatings
- Strong interface/adhesion
5. How do finish, hardness, and composition of the substrate contribute to wear resistance?
Surface finish: generally the smoother the surface the lower the wear
Hardness: increasing the difference in hardness between the two bearing surfaces will generally increase the wear
Substrate composition: The substrate needs to be able to support the film/coating, which is usually much harder than the substrate. Depositing a hard coating on to a soft film leads to premature failure since the harder, more brittle coating will not be supported by the substrate and will fail at lower loads. The adhesion of the coating or film to the substrate also is an extremely important property that controls the wear rate of the coating. No matter how wear resistant the film is, if the adhesion to the substrate is poor, the coating will fail prematurely. The film and substrate need to be considered as a continuum in the “coating system”. Each of these features, hardness and adhesion, will be controlled by substrate composition and its heat treatment. Normally a thin (50-100nm) adhesion layer of a reactive metal such as Ti, Cr, W, etc, is used to provide strong adherence between the substrate and the wear-resistant film. These thin films of Ti, Cr, W, etc, have the ability to react with reactive species, e.g., oxygen, adsorbed onto the substrate surface creating a strong bond at the interface.
Where possible, it usually is advantageous to provide ion mixing at the interface to improve adhesion. Ion mixing is created by increasing the ion bombardment energy sufficiently to implant depositing metal ions into the substrate to increase the bonding between the film and the substrate.
6. Which applications benefit most from coatings?
Those conditions that subject a surface of a component to extreme service conditions will normally benefit from a coating. Typical examples of such extreme conditions include: wear/abrasion, corrosion/oxidation, and loaded surfaces such as those encountered in stamping, forming, die casting, etc. With respect to the latter category of dies used in material processing and forming, there needs to be a minimum chemical reaction between the coating and the material being formed or processed. Normally, a much greater wear and degradation of the surface occur when chemical reactivity and abrasion occur together. This conjoint action of wear and corrosion is much more harmful than simply adding the effects of these two conditions acting alone.
7. What causes soldering in die casting molds?
The sequence of events leading to soldering and degradation of the die surface in Aluminum pressure die casting are outlined below:
- The oxide surface on the H13 tool steel is first exothermically reduced with aluminum, e.g, Fe2O3 + 2Al = 2Fe + Al2O3. The generation of heat from this alumino-thermic reduction reaction accelerates this and subsequent reaction stages.
- The liquid aluminum reacts with the nascent Fe formed from stage (1) to produce a series of Fe-Al intermetallics, e.g. Fe + Al = FeAl. This reaction is also exothermic, increasing the local temperature of the die surface, which again can accelerate this and subsequent reaction stages.
- Stage (2) occurs only when the die temperature is above a certain critical temperature (Tcrit), that generates a liquid reaction product from stage (2)
- The brittle Fe-Al based intermetallics formed from stages (2) and (3) break off the die surface leaving a defect in the die surface
- The embrittling formation of Fe-Al intermetallics also can lead to increased cracking in the H13 die surface. This chemical cracking is likely to exacerbate thermal fatigue cracking produced due to thermal cycling alone
The mechanism of soldering when coatings are used on dies is outlined below:
- The sequence of reactions for degradation of coated H13 die surfaces follows a similar sequence to that proposed above, with the exception of stage (1).
- However, once the die coating has been damaged or fractured, the sequence of reactions follows stages (2) to (5) above, resulting in extensive chemical pitting of the H13 substrate.
- Therefore, the preservation of the die coating is essential to extending die life and improving die performance.
- This conclusion means that die cleaning must be conducted in a manner that does not damage the die coating, e.g., using a cleaning cloth or brush soaked in caustic soda to clean off any solder from the die surface rather than using an abrasive stone.
- However, coatings can extend the life of dies used in aluminum pressure die-casting considerably.
8. How can coatings prevent soldering?
Coatings must minimize wetting/chemical interaction between the liquid aluminum and the working surface of the coating system. The coating also must provide superior wear resistance and exhibit good adhesion to the die substrate.
9. What are the characteristics of a good coating?
The following properties are required in a good coating system:
- Minimum residual stress; this can be a problem to control when the coating is used in service conditions that involve thermal and load cycling.
- Good tribological properties that include a favorable combination of relatively high hardness and wear resistance coupled to a low coefficient of friction (COF) and high toughness.
- Good oxidation/corrosion resistance if used in service conditions that can lead to a reaction between the environment and the film or coating. This latter condition requires that the coating exhibits low wettability/solubility with the material being processed.
- Good adhesion to the substrate
10. Why do coatings fail?
The reason why coatings fail will depend upon the service conditions and the properties of the coating in those service conditions. But, in outline, coatings fail for the following reasons:
- Poor wear resistance, adhesion, and oxidation/corrosion resistance.
- High reactivity with a material being formed.
- Poor design and coating “architecture” in which stresses are allowed to build up due to cycling conditions, etc, sharp corners/edges, and inappropriate film chemistries and microstructures.
- Misuse, such as inappropriate cleaning techniques (using abrasive stones instead of cleaning with brushes soaked in a solvent), mechanical damage in handling or transportation.
11. How does PVD CrN compare to other coatings?
It depends upon the application. In Al die-casting CrN performs as well as if not better than most coatings. However, CrN coatings can differ substantially in their wear behavior depending upon the coating architecture, chemistries used, adhesion to the substrate, and method of deposition and the extent of ion bombardment used.
12. What has been your experience with Phygen’s patented FortiPhy™ XVD coatings?
In aluminum die casting, the Phygen FortiPhy™ XVD coating has performed extremely well, exhibiting good adhesion, low wettability, and high wear resistance.
13. When soldering occurs, what are your recommendations for removing it from coated pins?
Do not use abrasive stones. A 4-micrometer thick coating is easily removed when polishing with abrasive stones. There is a need to use a new die cleaning practice that involves cleaning the surface of the die (coating) with a dilute sodium hydroxide solution applied with a paintbrush.