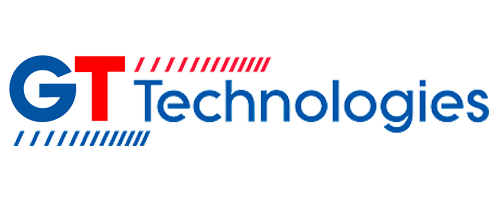
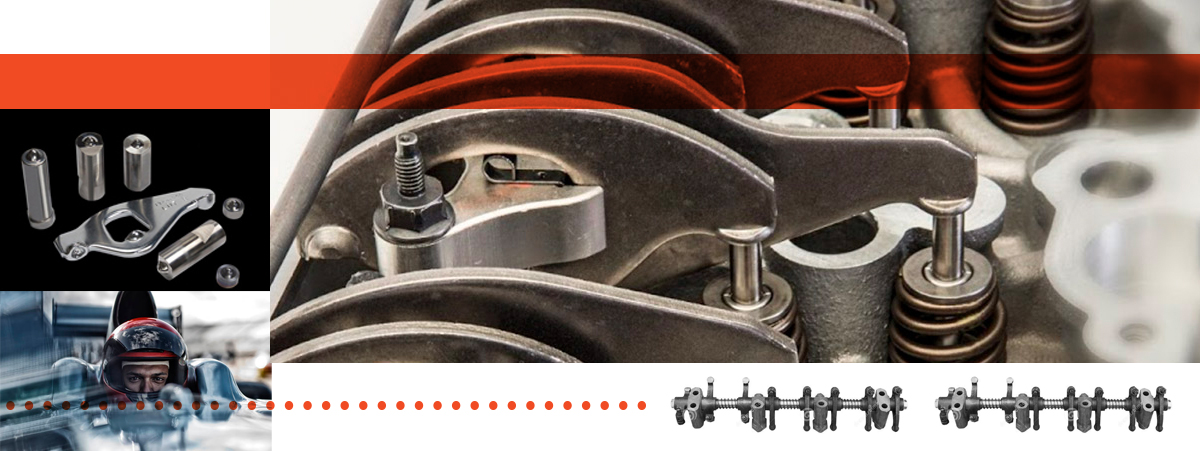
PROBLEM
GT Technologies supplies valve train component systems with high-quality surface finishes for automotive applications, commercial diesel engines, and performance racing engines. Its Toledo Technologies division has been working to upgrade several stamping operations: improving surface finishes, minimizing tool breakage, increasing lubricity and reducing lead times to repair or replace tools, which can take up to 10 weeks.
Solution
By switching from carbide to Phygen FortiPhy XVD, the company improved lubricity and surface finishes, and significantly reduced tool breakage and turnaround times. Toledo Technologies now uses FortiPhy XVD in prototype tooling. Prototypes go through rigorous testing to validate design. Even one week can make the difference between landing a new contract and missing a deadline.
It really is possible
more units
Where double-coated carbide tools produced only 135,000 parts before repair or replacement, tool steel coated with FortiPhy XVD punches produced 215,000 parts.
less lubricant
By using FortiPhy XVD, Toledo Technologies uses 25 percent less lubricant with no difference in part quality or tool wear.
“We were looking for a solution to our problems. Other surface treatments did not give us the results that FortiPhy XVD did. Because we’re running millions of parts, the fewer tooling changeovers we need, the better off we are.”