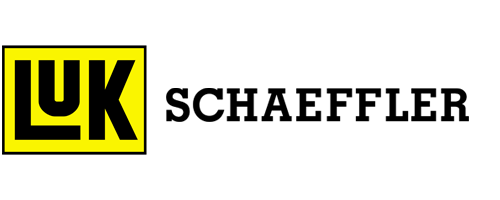
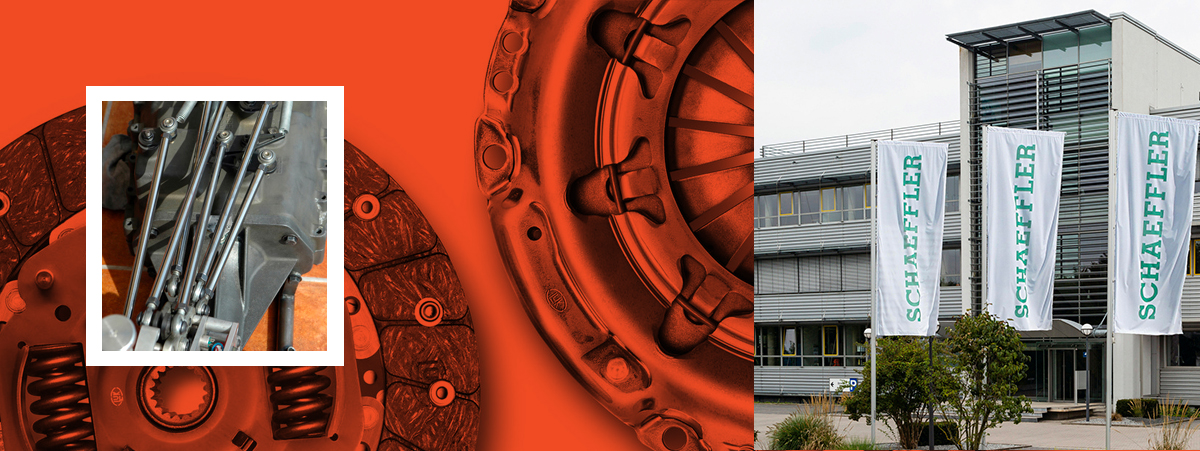
PROBLEM
LuK USA stamps steel from 0.5mm to 7mm thick to make transmission components for cars and light trucks. Sometimes 4mm thick steel becomes distorted when the outer bodies of torque converters are drawn. There’s so much force on the drawn steel that it’s polished or smeared from the die, which is a clear indication of extreme pressure.
Solution
One part required a coated die because the operation was so difficult. Even with TiN physical vapor deposition coating, the die had to be hand worked after every 500 pieces to bring it back into specification. Another PVD coating failed after 1,200 pieces. Once LuK tried FortiPhy™ XVD technology, the die yielded 38,000 pieces.
It really is possible
“Up until just recently, our only choice for forming steels was to use chemical vapor deposition (CVD) coating,” says Paul Gray, section leader. “But now, with FortiPhy XVD, a comparatively cold process (950°F), there’s no reason to worry about die movement, such as die or punch parts growing from the process and later having to re-cut them.”
productivity increase
“In high-pressure squeezing areas, FortiPhy XVD surface treatment is about the best for punching or blanking operations, as well as for trim dies.”