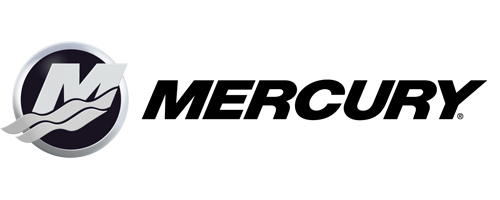
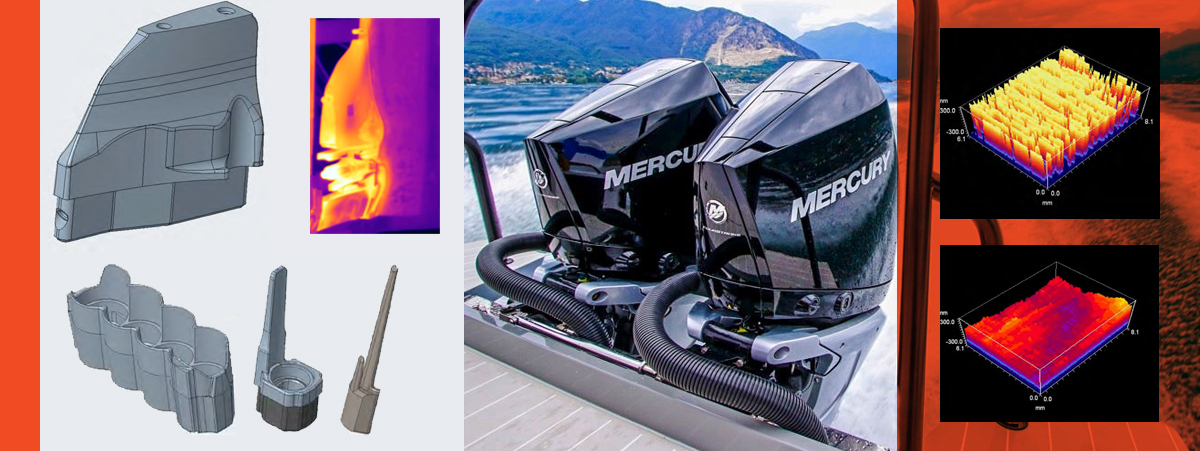

PROBLEM
Mercury Castings uses die inserts with physical vapor deposition (PVD) coatings in more than 60% of its dies. Some new inserts that were carefully prepared, with diamond polishing and PVD coating, would stick in the part during early use. Mercury asked Phygen to help find a better method.

Solution
Working together, Mercury and Phygen analyzed these die inserts. They checked surface roughness using an optical profilometer to compare 220 draw stone (rough) and diamond (smooth) polishing methods, and recorded a thermal image of a gearcase die that contained multiple inserts. They noted that the die inserts performed differently depending on their surface finishes and working temperatures.

It really is possible
Applying different surface treatments before coating improved performance even further. Die inserts that reach higher temperatures in use worked best with a smoother diamond finish; those that run cooler had optimal results with a rougher draw finish. FortiPhy™ XVD technology helped reduce soldering, allowed higher cycle speeds, and extended wear life for all the die inserts tested.
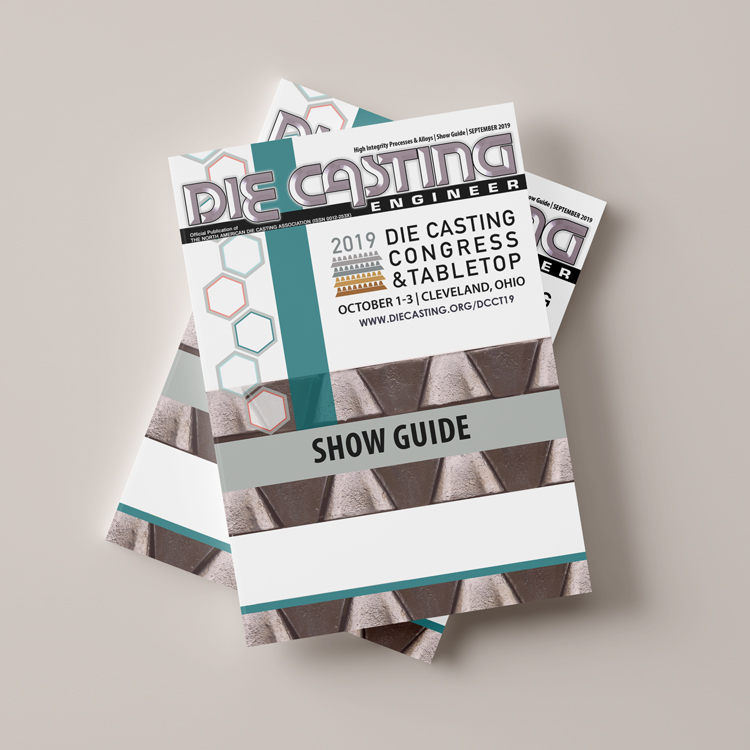
SEE FULL ARTICLES IN
DIE CASTING MAGAZINE
Surface treatments applied before coating affect the performance of die inserts at different temperatures. By applying the right finishes, Mercury now avoids break-in periods that can delay or interrupt regular production flows.